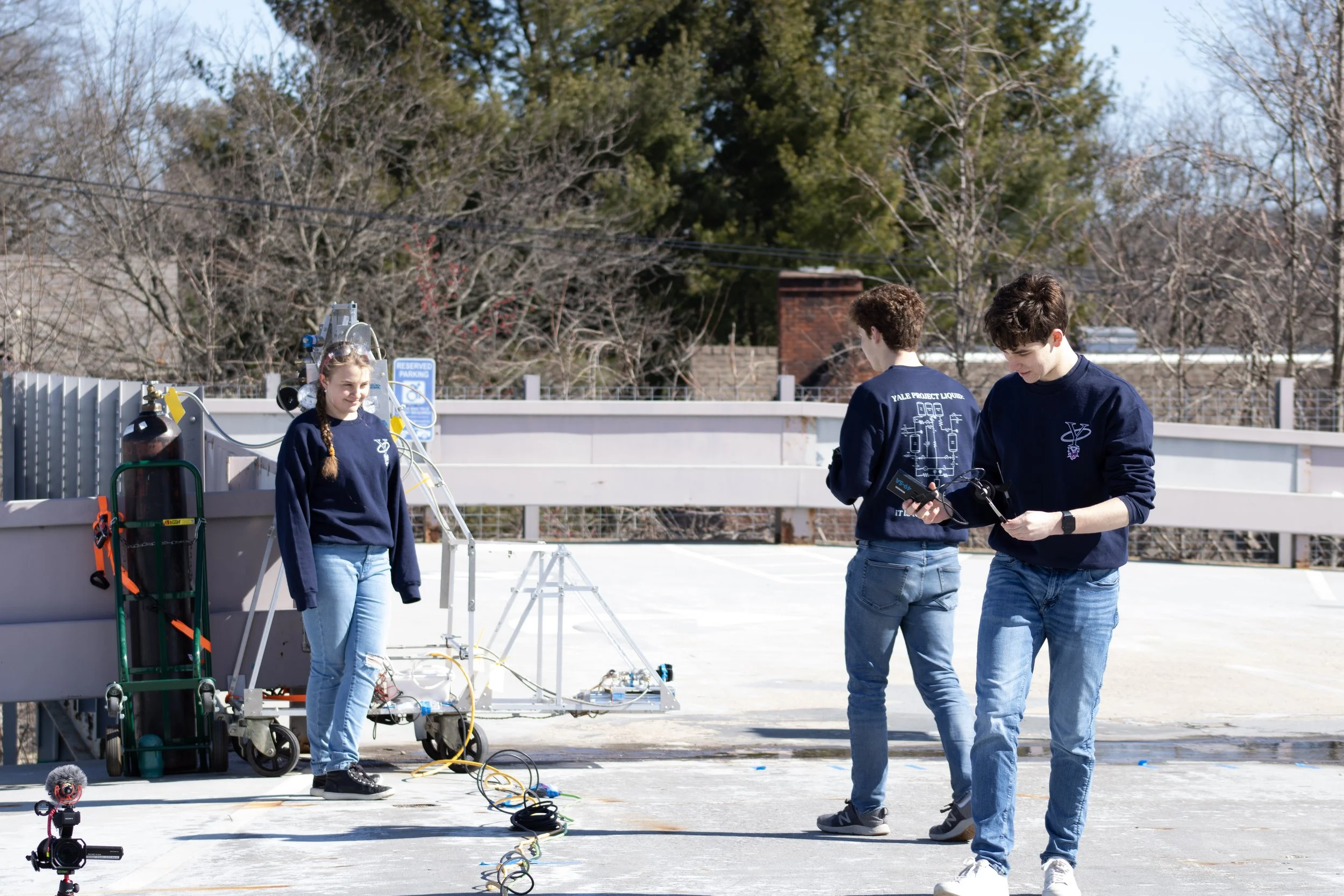
PROJECT LIQUID
PROJECT LIQUID
Yale Project Liquid is the first undergraduate initiative at Yale and in the Tri-State Area to develop an engine capable of liquid propulsion as designed. As the lead of the 30-person team in 2022 - 2023, I led the group through the inaugural build and hazardous pressure test of a bi-propellant liquid rocket engine at Yale. Now, I am the 2023-2024 Safety and Testing Lead.
ITERATIVE TESTING
As the first collegiate bi-propellant liquid rocket engine at Yale, I’ve worked hard to keep relevant stakeholders informed of the team’s design and ensure that safety and regulations can be controlled while promoting a high-frequency testing environment.
• Successfully re-opened and sustained talks for static fire permission with school administration after a year-long hiatus on discussion attempts by former leads.
• Found a suitable test site location for a static fire; two years of former leads and safety officers could not find this.
• To compensate for limited university subject expertise for liquid propulsion, I compiled documentation on hazardous propellant regulation, worked on implementing ASTM G93 Lox Cleaning, made a terrain-aware blast radius solver, and more. Additionally, I worked with multiple industry experts to incorporate their feedback and presence into routine design and safety reviews.
YENGINE 1.0 CONTRIBUTIONS
Technical Contributions:
• Designed the architecture for the fluid supply system, considering chemical compatibility, rated pressures, and galvanic corrosion on a part-by-part basis.
• Implemented a late-stage design iteration for the test stand chassis, featuring a steel beam running end-to-end, introducing rigidity and deflection for the three-part assembly of the fluids walls, electronics bay, and the forward-protruding thrust chamber module. Larger wheels to respond to transport logistics between the maker space and storage closet, using a steel u-channel.
• Reduced system complexity by consolidating COTS usage and unifying nominal piping size
Operational Contributions:
• Discovered, quoted, and shipped two tanks, seven valves, and most sensors. Was the sole point of purchasing 100% of system components, discounted parts by thousands of dollars cumulatively. Created an automated part traceability system, assigning each purchased and manufacturing component a unique identifier that could track part lifetime from CAD to the installation
• Coordinated the first hazardous pressure test of the team by working with Yale Environmental Health and Safety, the Deputy Dean of the School of Engineering, and other parties.